What Is a Tube Furnace?
A common inquiry in heat treatment circles is, "What is a tube furnace?" A tube furnace is a specialized furnace designed to heat materials in a controlled and uniform manner over a significant length. Tube furnaces encompass the material within a cylindrical tube, ensuring a consistent temperature profile along the length of the tube. This design is instrumental for various applications such as material synthesis, heat treatment and chemical vapor deposition, where a uniform temperature across the material is crucial for accurate and reliable results. There are three types: rotary tube furnaces, horizontal tube furnaces and vertical tube furnaces.
Tube Furnace Design and Components
The exterior structure of a tube furnace is crafted from robust, heat-resistant materials, ensuring durability – a critical aspect for enduring the high-temperature operations encountered in industrial settings. At the heart of the tube furnace lies the cylindrical tube, which is the core component housing the material to be heated. This tube is constructed from ceramics or other materials known for their heat-resistant properties. Encircling the cylindrical tube are the heating elements. The design of these elements, coupled with their strategic positioning around the tube, guarantees a uniform temperature profile.
Advantages of a Tube Furnace
- Precise Temperature Control: The design facilitates precise control over the temperature along the length of the tube, which is essential for many applications.
- Uniform Temperature Distribution: The cylindrical design ensures a uniform temperature profile, which is crucial for processes requiring consistent heating.
- Adaptability to Different Atmospheres: Tube furnaces can be designed to operate under various atmospheres, making them versatile for different processes.
Common Tube Furnace Uses
The operational advantages translate into a wide range of tube furnace uses across different industries.
- Material Synthesis and Processing: Ideal for processes requiring a consistent temperature over a significant length, enabling the accurate synthesis and processing of materials.
- Heat Treatment: Utilized for heat treatment processes where uniform heating is crucial for achieving the desired material properties.
- Chemical Vapor Deposition: Often used for chemical vapor deposition processes due to the constant temperature and the ability to control the atmosphere, ensuring precise deposition of materials.
Considerations When Choosing a Tube Furnace
Selecting a suitable tube furnace requires careful consideration to ensure it meets the specific requirements of the intended applications. This section discusses the key considerations when opting for a tube furnace.
- Size and Capacity: Available in various lengths and diameters to accommodate different material sizes and quantities, ensuring a perfect fit for the application at hand.
- Temperature Range: Selection based on the maximum and minimum temperatures required for the intended processes ensures the furnace meets the thermal requirements.
- Atmosphere Requirements: Consideration of the atmosphere control capabilities based on the needs of the specific processes, facilitating a controlled environment for optimal results.
What Is a Muffle Furnace?
For individuals involved in industrial and laboratory settings seeking to achieve high-temperature conditions for various applications, "What is a muffle furnace?" is a common query. Muffle furnaces are a type of furnace where the material to be heated is placed inside a chamber that's separated from the fuel and any combustion gases. This design ensures a controlled, clean and consistent heating environment, making muffle furnaces ideal for numerous heat treatment processes, ashing and ceramics processing, etc.
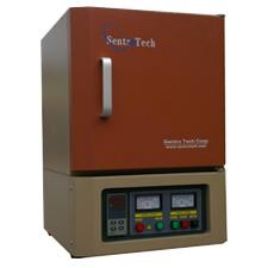
Muffle Furnace Design and Components
A muffle furnace comprises three primary components: the exterior structure, the heating chamber or "muffle," and the heating elements alongside temperature control systems. The exterior is constructed from robust, heat-resistant materials like steel, ensuring durability and safety. The heart of the furnace is the "muffle" — an insulated chamber that houses the material to be heated. The heating elements, typically made from resistant materials like Kanthal or silicon carbide, surround the muffle and provide the necessary heat. Modern muffle furnaces have digital temperature control systems for precise temperature setting and monitoring.
Operational Mechanism
The operational mechanism of a muffle furnace is straightforward yet effective. The heating elements generate warmth, while the insulation retains the heat. The muffle's design ensures a uniform temperature distribution, which is crucial for consistent results in heat treatment processes. Temperature control systems allow for precise setting and temperature monitoring, ensuring that the desired heating conditions are accurately maintained throughout the process.
Advantages of a Muffle Furnace
Muffle furnaces have numerous advantages, making them a preferred choice for various high-temperature applications. This section outlines the key benefits of muffle furnace use in industrial and laboratory settings.
- Ease of Use: The simple design and operational mechanism of muffle furnaces contribute to their ease of use. Digital control systems further simplify the process, allowing for accurate temperature setting and monitoring, making it convenient even for individuals with minimal technical knowledge.
- High-Temperature Capabilities: Muffle furnaces reach high temperatures ranging from 1000 to 1200 degrees Celsius – or even higher in advanced models. This high-temperature capability is crucial for muffle furnace uses like ceramics processing, heat treatment and ashing.
- Robustness and Durability: Because they're constructed of high-quality, heat-resistant materials, muffle furnaces withstand the corrosive and harsh environments often encountered in industrial settings. Their robustness and durability ensure a long operational life, making them a cost-effective choice for many applications.
Common Muffle Furnace Uses
A muffle furnace has uses in many fields thanks to its versatile design and high-temperature capabilities. This section explores some common uses of muffle furnaces across different industries.
- Ashing: In laboratories, a primary use of a muffle furnace is the ashing process, which determines the ash content of samples. This is crucial in fields like environmental testing, food testing and materials analysis.
- Ceramics Processing: The ceramics industry relies heavily on muffle furnaces for firing and hardening ceramic products. The high-temperature capabilities and uniform heating environment ensure the desired material properties are achieved.
- Heat Treatment: Another use of muffle furnaces is heat treatment processes in the metallurgical and material science fields. They're used to alter the physical and chemical properties of materials, enhancing their performance and usability.
Considerations When Choosing a Muffle Furnace
Choosing the right muffle furnace requires a thorough understanding of the various considerations involved. This section discusses key factors to consider when choosing a muffle furnace for your specific application.
- Size and Capacity: Muffle furnaces come in various sizes to accommodate different material quantities. When selecting a muffle furnace, consideration of the space available and the load capacity required for specific muffle furnace uses is crucial.
- Temperature Range: The selection of a muffle furnace is based on the maximum temperature required for the intended application. It's essential to ensure the furnace can achieve and maintain the necessary temperature for the processes involved.
- Atmosphere Control: Some muffle furnace models have controlled atmosphere capabilities for specialized applications. This feature allows for the management of the atmosphere within the muffle, which could be crucial for certain heat treatment processes or materials research.
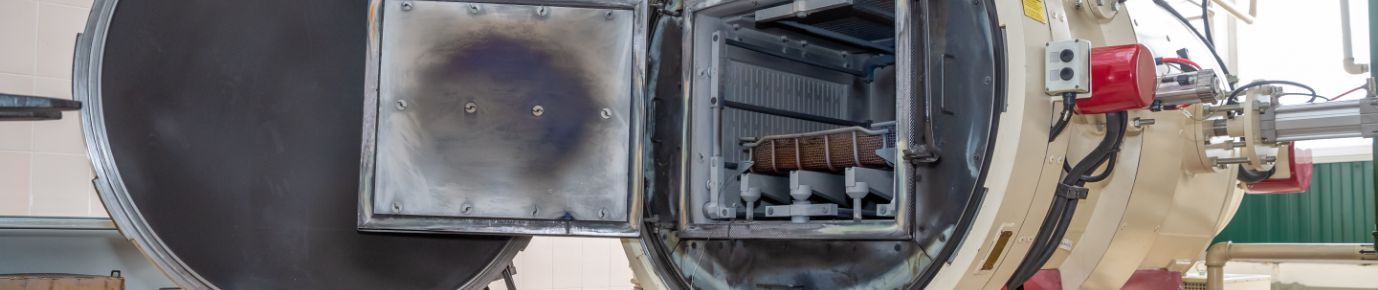
Tube Furnace vs. Muffle Furnace: Frequently Asked Questions
Below, we've answered some common questions to help you choose between a tube furnace vs. muffle furnace.
How Does a Muffle Furnace Work?
A muffle furnace operates by enclosing the material to be heated in a chamber, separated from the heating elements, ensuring a clean, controlled heating environment. The heating elements generate heat, which is retained within the insulated chamber, providing a uniform temperature for processes such as heat treatment, ashing and ceramics processing. Modern muffle furnaces have digital control systems for precise temperature regulation, making them convenient for various industrial and laboratory applications.
How Does a Tube Furnace Work?
A tube furnace works by heating materials placed within a cylindrical tube, with heating elements surrounding the tube to provide uniform heating along its length. The design allows for precise temperature control and uniform temperature distribution, essential for material synthesis and heat treatment processes. Digital control systems enable accurate temperature setting and monitoring, making tube furnaces adaptable for applications requiring controlled heating over a significant length.
What Is the Difference Between a Tube Furnace vs. Muffle Furnace?
A tube furnace and a muffle furnace differ mainly in design and heating mechanism. A tube furnace encases materials within a cylindrical tube for uniform heating along its length, ideal for material synthesis and heat treatment. Conversely, a muffle furnace isolates materials in a chamber from combustion gases, providing a controlled heating environment suitable for batch processing tasks like ashing and ceramics. The choice between the two depends on the application's specific requirements, including temperature uniformity and material dimensions.
Order Your Tube Furnace or Muffle Furnace From Sentro Tech Today
Your quest for a high-quality furnace tailored to your specific industrial or laboratory needs ends at Sentro Tech. With a rich legacy in crafting state-of-the-art tube furnaces and muffle furnaces, Sentro Tech is your go-to destination for acquiring a furnace that stands the test of time and efficiency. Reach out, and our team of experts will guide you in selecting the furnace that aligns seamlessly with your requirements.
Contact UsHigh-Temperature Furnaces, Kilns, Ovens & More | Sentro Tech
From box furnaces and rotary tube furnaces to compact laboratory furnaces and large-scale production ceramic kilns to vacuum furnaces, every Sentro Tech furnace is engineered to provide exceptional value, extended durability and the precise results you seek.