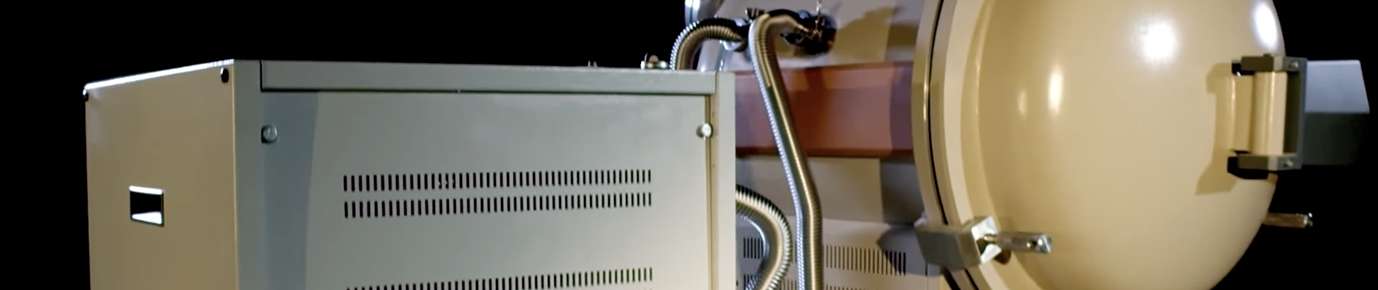
What Is Sintered 3D Printing?
Sintered 3D printing, also commonly referred to as Direct Metal Laser Sintering (DMLS), is a metal-additive manufacturing process. Sintered 3D metal fabrication uses laser technology to scan and selectively fuse metal powder particles. The selective fusing bonds the particles together during these processes to build metal parts layer by layer. In DMLS 3D metal fabrication, the powder is composed of metal alloys with variable melting points that can fuse on a molecular level at certain elevated temperatures.
Metal 3D Printing Steps Explained
The 3D metal printing process starts with a 3D CAD model of a part design. This can be anything from an air intake for a race car to a highly intricate part to be used in a metal watch – the design is up to you. Unlike polymer powder bed fusion processes, 3D-printed structural parts are attached to the sintering furnace through support structures. Support structures are built from the same materials as the parts and help mitigate any possible warping or distortion in the high-process temperatures.
The basic fabrication process for creating 3D-printed structural parts is as follows:
- The CAD model is digitally separated into layers. At the same time, any needed support structures are added to aid in the 3D printing manufacturing process.
- The powder bed is filled with a high-strength alloy. Generally, this high-strength alloy will be one of the following materials: aluminum, titanium, Inconel, stainless steel or cobalt chrome. A thin layer of the selected alloy is then distributed across the build platform.
- From there, the build begins. A high-powered laser draws the bottom layer of the batch, along with any temporary support structures necessary to support the 3D printing sintering.
- A rubber wiper will then scrape another layer of metal powder across the parts, and the lasering process is repeated again and again until completion.
- Once complete, the part is removed from the build chamber along with the build supports. The 3D-printed structural parts may then be further processed per customer requests.
After the 3D printing manufacturing process is complete, the parts will be fully encapsulated in metal powder. Once the bin cools to room temperature, the excess powder can be manually removed. From there, the parts will be ready for post-processing. Post-processing treatments can include heat treatment and detachment from the build plate via cutting, machining, hot isostatic pressing or solution annealing.
Take Your First 3D Printing Process Steps With Sentro Tech
Sentro Tech is a leading manufacturer of custom high-temperature sintering furnaces for your 3D metal fabrication and printing needs. We carry a full selection of standard models capable of reaching temperatures up to 1700°C, as well as a full range of customization options for your specific needs. Choose a sintering furnace that will best support your 3D printing processes. We also offer furnace heating elements like high-temperature heating elements, braided contact straps, MoSi2 heating elements, and more. Choose Sentro Tech.
Shop Sintering Furnaces3D-Printed Structural Parts – Application & Uses
The possibilities of 3D metal printing processes have made the technology extremely popular in manufacturing complex parts using high-performance metals and alloys. The areas that benefit most from sintered 3D printing include the medical, dental and aerospace industries. These industries often require parts made from high-performance or exotic materials that cannot be manufactured with conventional metalworking technology.
Medicine
Custom prosthetics and customized implants can be modeled and printed, with 3D-printed structural parts made from titanium alloys replacing small portions of bone lost to accident or disease. Thanks to the 3D metal printing process, parts have high strength, are resistant to internal attacks from the body and are porous enough that bone can quickly grow into the prosthetic structure. Not to mention, each prosthetic is unique to the individual patient.
Dentistry
Sintered 3D printing can make dental implants, prosthetics, bridges, crowns and partial dentures. These can be easily modeled to a specific patient and fabricated from high-strength materials. The 3D metal printing process can quickly deliver custom-fit, high-strength, durable parts to patients.
Aerospace
3D metal fabrication can create parts that are vital in commercial aircraft and rockets, from brackets to highly complex turbine parts. With the 3D metal printing process, scientists can even produce complete rocket exhaust systems. The possibilities only continue to grow.
Speak to Sentro Tech About 3D Metal Fabrication Today
Now that you know more about metal 3D printing steps and processes, it's time to put them into practice in your own laboratory or production facility. Custom-built or standard sintering furnaces from Sentro Tech offer a wide range of capabilities to meet your specific needs. With quick heat-up and cooldown, temperature accuracy and uniformity, customizable temperature ranges and dimensions and much more, sintering furnaces from Sentro Tech are the smartest way to achieve your 3D printing manufacturing processes. View our entire selection and request a quote today. Or, if you have any questions, please contact us at any time. Our expert team is standing by, ready to assist.
Request a Quote