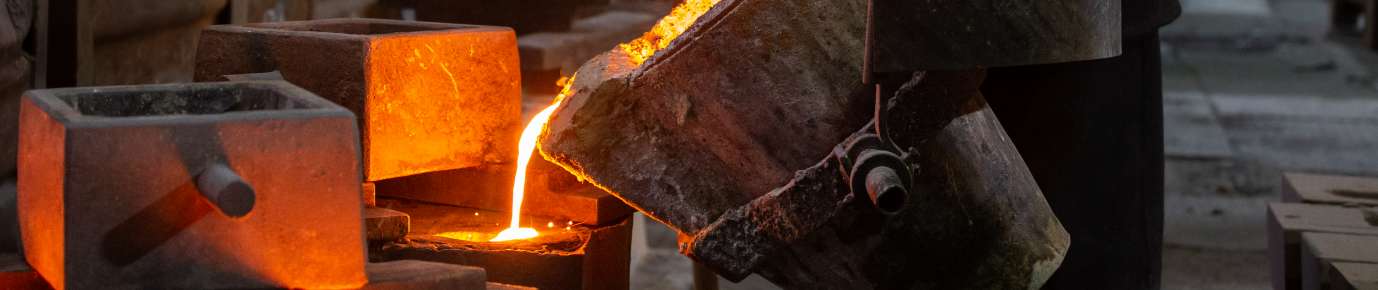
The History of Casting Foundries
While the casting process is thousands of years old, the first industrial foundry started operating in the late 15th century in Europe. Early industrial foundry work centered on manufacturing cannon balls, cannons and iron and bronze bells. As colonists and pioneers moved across North America, foundries produced the tools, horseshoes and rail tracks they needed to conquer new lands.
A modern casting foundry is highly mechanized, using specialized casting machines and foundry equipment, including cupola, induction, crucible and electric arc furnaces.
What Does a Foundry Do?
Today's industrial foundry manufactures much more than iron horseshoes. In fact, the United States produces 9.8 million metric tons of metal castings annually. Besides iron, the materials used to make modern foundry castings include steel, aluminum, bronze, brass, copper and a wide array of alloys.
Nearly every industry relies on metal castings, including dental and medical, aerospace, power generation, auto making, sports equipment, consumer products, defense, dairy and more. Parts can weigh from a fraction of an ounce to several tons. Applications range over a wide variety of products, such as:
- Boat exhaust manifolds
- Dental brace components
- Cookware, like brownie pans and cast iron skillets
- Cake donut dropper frames
- Campground water pumps
- Automobile control arms
- Disc brake brackets and anchors
- Dishwasher motor housings
- Fire hydrants
- Golf clubs
- Helicopter components
- Barbecue grills
High-Temperature Furnaces That Get the Job Done
Custom high-temperature casting and foundry furnaces are our specialty. As a leading furnace manufacturer, Sentro Tech can customize any furnace, including muffle furnaces, to meet our customers' specific requirements. We understand your needs and respond with the highest level of products and customer service. Find out today what a Sentro Tech furnace can do for your operation.
Contact Us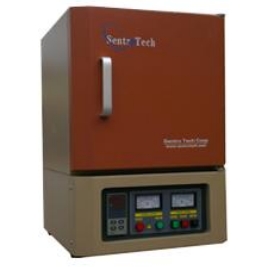
What Is the Foundry Process?
Foundry metal casting consists of several basic steps. The first phase in the foundry process is patternmaking, which uses a wood or metal replica of the part to create the mold for the component. Once the mold is made, a furnace heats the metal until it's molten, and the liquid metal is poured into the molds. The molds are cooled, and, after the parts solidify, they're removed from the mold.
Several secondary finishing processes, such as heat treating, grinding, polishing and fabricating, complete the part and ready it for inspection and delivery. Besides furnaces, foundry operations use a wide range of industrial machines, including cranes, forklifts, ladles and transfer vessels.
How Are Foundries Powered?
In the earliest foundry operations, manually operated bellows fanned the flames that melted metal for casting. Later foundries used steam power, while today's industrial foundry uses electricity to power its furnaces.
Foundry design practices take into account the extreme temperatures and hazards associated with metal casting and incorporate various fire-retardant materials and devices. For instance, many foundry floors are made of high-temperature concrete, which is rated for thermal shocks. Most foundries have high ceilings to promote air circulation and help mitigate the high ambient temperatures resulting from foundry work.
Rely on Sentro Tech for Your Muffle Furnace Needs
The modern foundry process demands the highest level of quality. Custom high-temperature muffle furnaces from Sentro Tech deliver that quality and more. All of our models offer excellent temperature control and uniformity and superior energy efficiency. With Sentro Tech ovens, you can lower the costs of small-scale production and laboratory environments. Contact us today to learn how.
Contact Us